The BMW Group continues to advance its industrial-scale 3D printing
23 Dec 2020|1,261 views
The BMW Group is taking the next step in the systematic integration of additive manufacturing. The aim is to scale additive manufacturing up to industrial levels and firmly establish it in various areas - primarily vehicle development and production - to positive economic effect.
The BMW Group benefits fully from the advantages of the technology, which offers fast availability of components, flexible component design, and the ability to manufacture parts without elaborate tools.
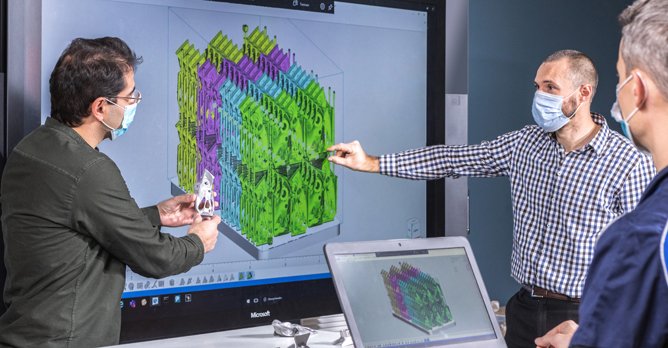

The components concerned are for the vehicle body and passenger cell, and are highly functional and rigid. The process for manufacturing them was developed and prepared for application in automotive production by the BMW Group, at the company's own Additive Manufacturing Campus, which also produces polymer parts by multi-jet fusion and selective laser sintering.
At BMW Group Plant Landshut, metal parts are currently made by laser beam melting. In production, the metal 3D-printed components are fitted to car bodies in an almost entirely automated process. Polymer components from the Additive Manufacturing Campus and the metal substrate for the trim panel are fitted in the automobiles.
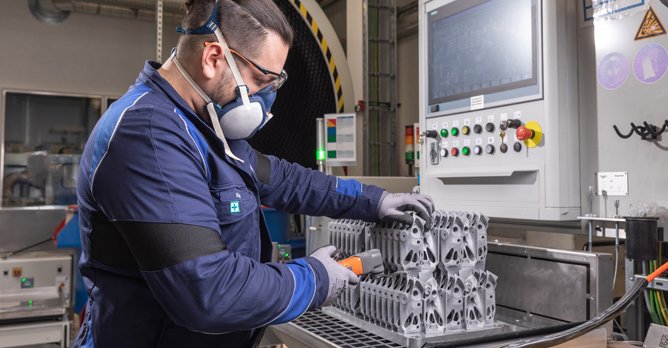

Parts that had previously been virtually impossible to realise are engineered by generative design, which uses computer algorithms for rapid component development.
Many potential applications are only possible at all thanks to generative design, and 3D printing technologies are particularly suitable for creating their complex forms and structures, which were previously impossible to produce with conventional tools.
For the BMW Group, generative design resulted in topology-optimised solutions, where form and function have been significantly enhanced. The components are around 50% lighter than comparable conventional components and make the best possible use of the space available.
Since June the BMW Group has pooled its entire technology expertise at the Additive Manufacturing Campus just outside Munich. The new campus also provides training for associates from around the world to use the new technologies, and is the home of prototype component production.
At the moment the centre of excellence has up to 80 associates and already operates about 50 metal and polymer processing systems. A further 50-plus systems are operating at other production sites around the world.
The BMW Group is taking the next step in the systematic integration of additive manufacturing. The aim is to scale additive manufacturing up to industrial levels and firmly establish it in various areas - primarily vehicle development and production - to positive economic effect.
The BMW Group benefits fully from the advantages of the technology, which offers fast availability of components, flexible component design, and the ability to manufacture parts without elaborate tools.
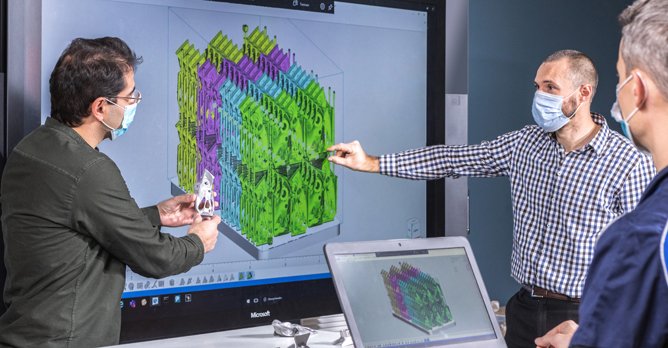

The components concerned are for the vehicle body and passenger cell, and are highly functional and rigid. The process for manufacturing them was developed and prepared for application in automotive production by the BMW Group, at the company's own Additive Manufacturing Campus, which also produces polymer parts by multi-jet fusion and selective laser sintering.
At BMW Group Plant Landshut, metal parts are currently made by laser beam melting. In production, the metal 3D-printed components are fitted to car bodies in an almost entirely automated process. Polymer components from the Additive Manufacturing Campus and the metal substrate for the trim panel are fitted in the automobiles.
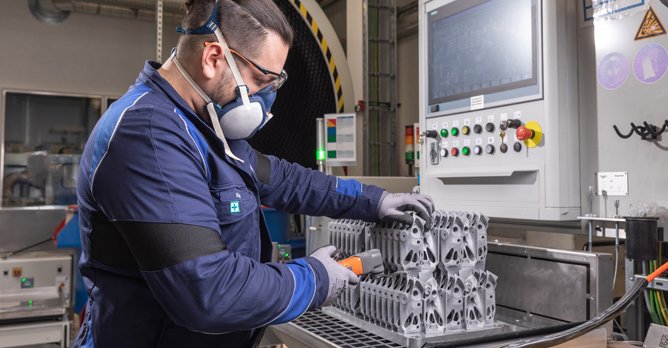

Parts that had previously been virtually impossible to realise are engineered by generative design, which uses computer algorithms for rapid component development.
Many potential applications are only possible at all thanks to generative design, and 3D printing technologies are particularly suitable for creating their complex forms and structures, which were previously impossible to produce with conventional tools.
For the BMW Group, generative design resulted in topology-optimised solutions, where form and function have been significantly enhanced. The components are around 50% lighter than comparable conventional components and make the best possible use of the space available.
Since June the BMW Group has pooled its entire technology expertise at the Additive Manufacturing Campus just outside Munich. The new campus also provides training for associates from around the world to use the new technologies, and is the home of prototype component production.
At the moment the centre of excellence has up to 80 associates and already operates about 50 metal and polymer processing systems. A further 50-plus systems are operating at other production sites around the world.
Latest COE Prices
April 2025 | 1st BIDDING
NEXT TENDER: 23 Apr 2025
CAT A$97,724
CAT B$117,899
CAT C$68,782
CAT E$117,002
View Full Results Thank You For Your Subscription.